
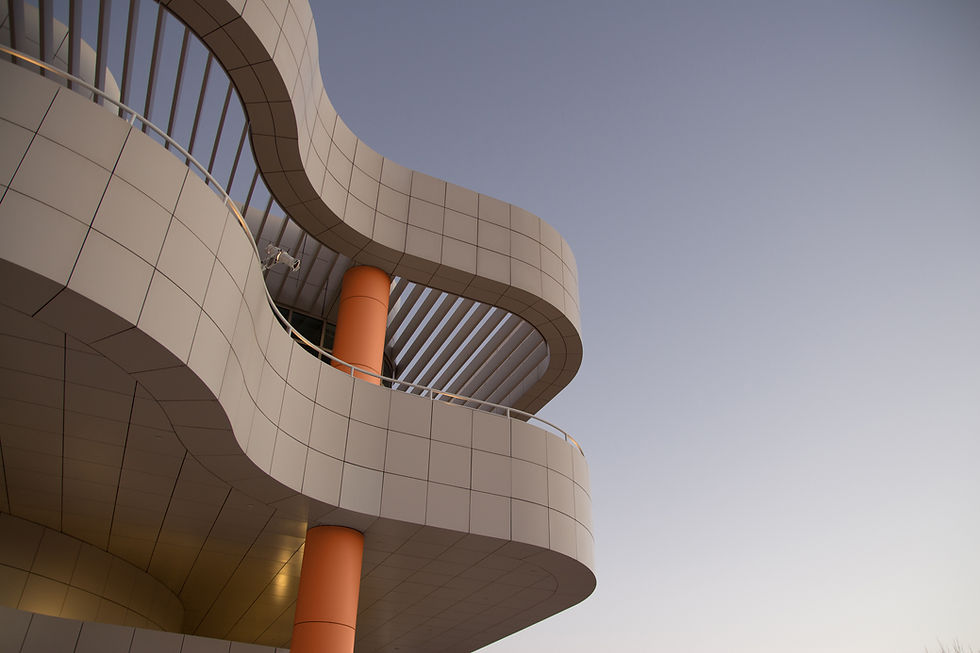
Safety Oversights Lead to Severe Injury at Steggles Pty Ltd: Lessons and Legal Consequences
Jul 11, 2024
3 min read
0
21
0
Case: SafeWork NSW v Steggles Pty Ltd [2024] NSWDC 217
Presiding Judge: David Russell SC [DCJ]
Prosecutor: Barrister Malcolm Scott
Defence: Barrister Patrick Barry
Outcome: Defendant Convicted, Conviction Recorded, Fined $160,000 + Costs
Introduction
Workplace safety is a critical component of operational protocols, especially in environments with high-risk machinery. The case of SafeWork NSW v Steggles Pty Ltd [2024] NSWDC 217 highlights the devastating consequences of safety oversights in a poultry processing plant. This article delves into the details of the case, the legal findings, and the lessons learned for enhancing workplace safety.
Case Overview
On 6 October 2020, Mr. Haraka Gatabishwa, a process worker at Steggles Pty Ltd, suffered a severe injury while performing housekeeping duties near the Overhead Shackle Conveyor Line and Hock Cutter at a poultry processing plant in Beresfield, NSW. In an attempt to reattach a chicken carcass to the conveyor line, Mr. Gatabishwa's hand was caught and subsequently severed by the rotating blade of the Hock Cutter. This incident brought to light significant safety failures at Steggles, leading to a prosecution under the Work Health and Safety Act 2011 (NSW) (WHS Act).
Legal Findings
The court found Steggles guilty of failing to comply with their work health and safety duty, thereby exposing Mr. Gatabishwa to a risk of serious injury or death. Key failures identified include:
Inadequate Guarding: The Hock Cutter and Conveyor Line lacked sufficient physical barriers to prevent accidental contact with moving parts.
Risk Assessment Deficiencies: Steggles failed to conduct comprehensive risk assessments that identified the hazards associated with the Conveyor Line and Hock Cutter, including the risk of workers becoming entangled in the machinery.
Lack of Safe Work Procedures: There were no enforced procedures prohibiting the operation of the Conveyor Line without proper guarding or interlocked barriers in place.
Insufficient Training and Supervision: Mr. Gatabishwa did not receive adequate training or supervision regarding safe work procedures around the Conveyor Line and Hock Cutter.
Decision and Penalty
The court convicted Steggles and imposed a fine of $160,000, reduced from an initial $200,000 due to an early guilty plea. Additionally, Steggles was ordered to pay the prosecutor's costs and 50% of the fine to the prosecutor, emphasizing the need for accountability and deterrence in workplace safety breaches.
Lessons Learned
The Steggles case underscores the critical importance of robust safety measures and adherence to safety protocols. Key takeaways include:
Effective Guarding: Installing adequate physical barriers around hazardous machinery is essential to prevent accidental contact and serious injuries.
Comprehensive Risk Assessments: Regular and detailed risk assessments are necessary to identify potential hazards and implement appropriate control measures.
Strict Enforcement of Safety Procedures: Developing and enforcing safe work procedures ensures that machinery operates only under safe conditions, reducing the risk of accidents.
Ongoing Training and Supervision: Continuous training and active supervision of workers are vital to maintaining a safe working environment and ensuring adherence to safety protocols.
Prompt Remedial Actions: Following the incident, Steggles took immediate steps to enhance safety measures, including installing a stainless-steel fixed guard fence around the Conveyor Line and Hock Cutter, updating risk assessments, and improving training programs.
Conclusion
The prosecution of Steggles Pty Ltd highlights the severe consequences of neglecting workplace safety. This case serves as a crucial reminder for all businesses to prioritize safety, conduct thorough risk assessments, implement effective control measures, and ensure continuous training and supervision of workers. By doing so, companies can prevent tragic incidents and foster a culture of safety and responsibility in the workplace.